Domenica 20 maggio ha rappresentato un giorno decisamente importante per due marchi prestigiosi dell’industria nazionale e per il mondo della batteria. La FBT di Recanati ha infatti ufficializzato con un grande evento gratuito l’acquisizione del brand DS Drum.
La FBT è un’azienda leader nel campo dell’amplificazione audio professionale, attiva a Recanati dal 1963: dopo gli inizi con la costruzione di amplificatori per chitarra, basso, tastiere e voce, ha ampliato man mano il raggio d’azione e può oggi legittimamente vantarsi di riuscire a supportare qualsiasi esigenza in materia di diffusione sonora, dal karaoke al live in un club, dall’amplificazione nei teatri a quella negli stadi e arene di grandi dimensioni, senza tralasciare i sistemi di diffusione in ambienti pubblici delicati quali ospedali, scuole o aeroporti, che abbisognano di particolari e delicate certificazioni.
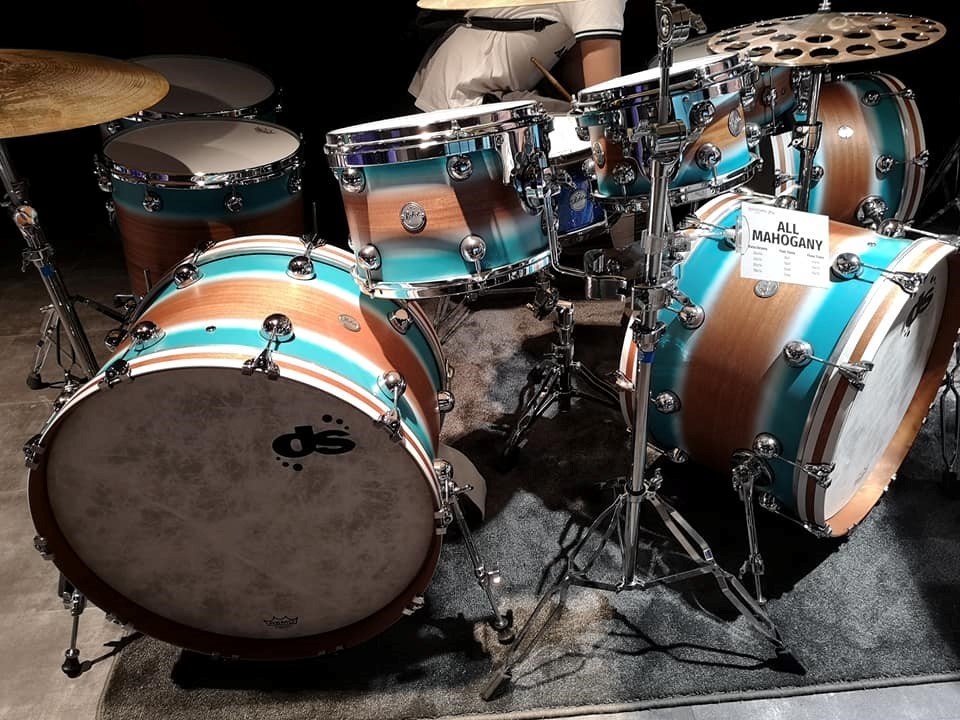
Ds Drum All Mahogany – Foto di Alessandro Dondi
Nel 1983 l’azienda di Recanati ha iniziato a cimentarsi anche nella distribuzione sul territorio nazionale di importanti marchi esteri, sempre nel mondo degli strumenti musicali: per restare nel nostro campo d’azione, FBT è da anni importatrice e distributrice esclusiva dei piatti Sabian e sino all’anno passato ha commercializzato in Italia i prodotti di un importante brand giapponese di batteria.
Nel 2017 ha acquisito lo storico marchio torinese DS Drum, sinonimo di batterie professionali italiane, creato nel 1995 da Luca Deorsola. E finalmente lo scorso 20 maggio il nuovo sodalizio è stato ufficializzato, dopo il trasferimento della DS da Torino a Recanati, in un padiglione apposito che sorge a pochi passi dal ‘cuore’ produttivo della FBT e accoglie sia i macchinari disegnati e utilizzati da Deorsola nella vecchia fabbrica sia altre macchine che è stato possibile acquistare grazie all’ingresso in FBT.
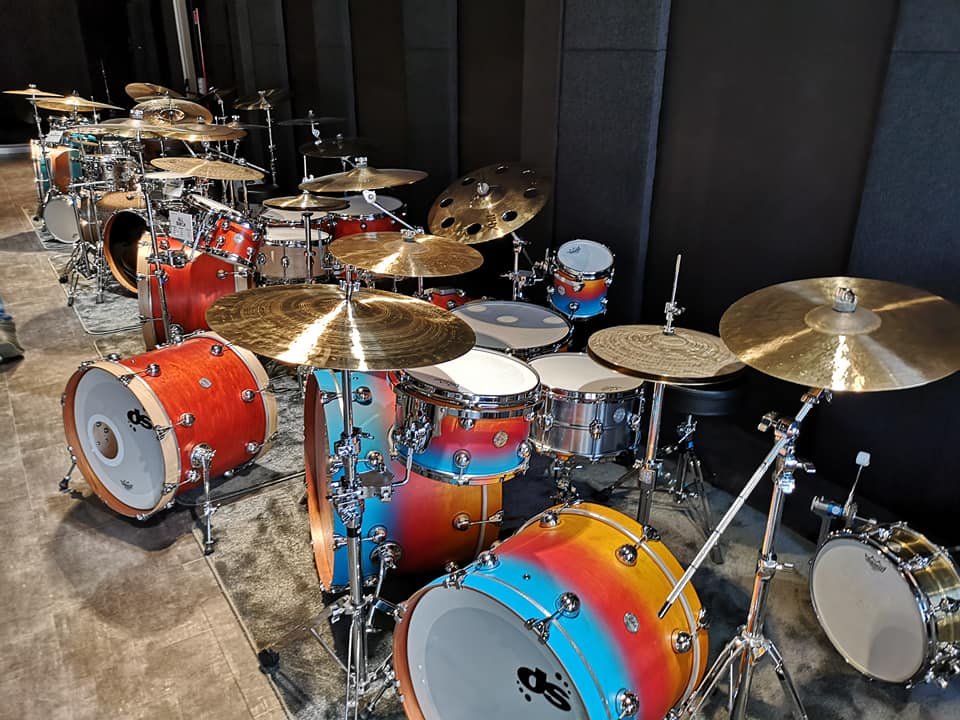
Show Room DS Drum – Foto di Alessandro Dondi
Nello stesso padiglione di via Paolo Soprani 2 ha sede il nuovo Show Room DS Drum, dove si trova esposto il meglio della produzione attuale. E alternandosi tra questo spazio e un palco appositamente allestito all’aperto domenica 20 maggio si sono esibiti alcuni tra i più noti e bravi endorser del marchio torinese, dall’attuale batterista di Jovanotti, Gareth Brown, a quello storico di Zucchero Adriano Molinari, passando per John Macaluso, Ernestico Rodriguez, Pier Foschi, Diego Corradin, Danilo Menna…
La giornata, a ingresso gratuito, ha visto l’inaugurazione del padiglione DS con tanto di taglio del nastro alla presenza delle principali autorità cittadine e la possibilità, per i visitatori, di fare un giro guidato nel padiglione adibito alla creazione da zero delle batterie DS Drum.
Il factory tour
Lunedì mattina, il 21 maggio, un nutrito gruppo di rivenditori al dettaglio e di addetti ai lavori ha potuto effettuare un approfondito Factory Tour condotto da Luca Deorsola, fondatore della DS Drum, oggi socio della FBT nonché direttore di produzione e responsabile dello sviluppo dei prodotti. Deorsola ha esordito affermando che, con il passaggio alla FBT, non è affatto cambiata la sua filosofia costruttiva, ma certo è migliorata per quanto riguarda gli aspetti più pratici della logistica e per la aumentata disponibilità di materiali e macchinari.
L’idea che ora può mettere in pratica è quella di produrre una batteria di qualità partendo da zero. La Rebel Custom Shop 2018 è quindi una versione ‘matura’ della batteria DS che Deorsola costruiva nel 1995, una sorta di prototipo al quale è in un certo senso tornato. In più l’esperienza pregressa e la disponibilità di locali, macchine e materiali garantiti da un’azienda quale FBT gli consentono oggi di offrire anche strumenti con tagli, spessori e finiture customizzate.
La Rebel Custom Shop realizzata negli stabilimenti della FBT di Recanati vuol essere una batteria di qualità che sia versatile, facile da accordare e resistente per i tour e dall’estetica che non passi inosservata. Per la sua realizzazione si parte dall’acquisto di materia prima di qualità dalle aziende (poche al mondo) che commerciano legno derullato, ossia ‘sfogliato’, e non tranciato: ciò consente di ottenere dei ‘fogli’ di legno perfettamente dritti della lunghezza di circa tre metri. Quanto alle essenze più utilizzate, dall’Africa c’è il mogano, dalla Scandinavia la betulla, dall’America l’acero e dall’Italia il faggio.
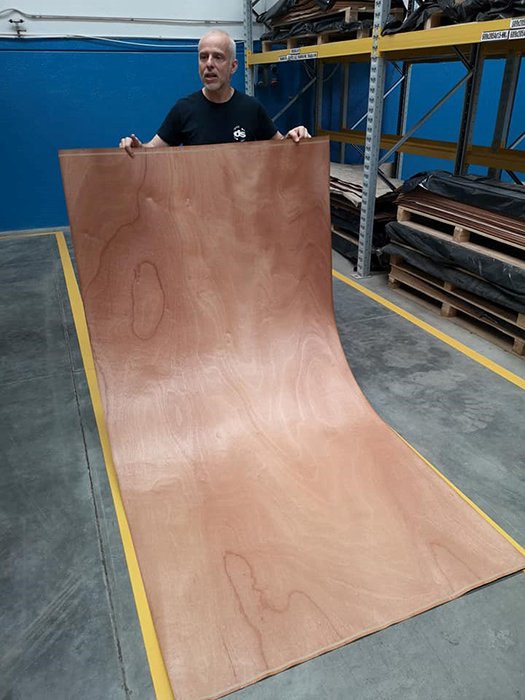
Un foglio derullato – Foto di Alessandro Dondi
Nel capannone in cui avviene la produzione i fogli di legno ‘riposano’ rimanendo costantemente a una determinata temperatura grazie a un impianto di umidificazione che a a questo scopo provvede a intervalli regolari a vaporizzare con dell’acqua gli ambienti.
Il fusto della batteria Rebel Custom Shop è frutto di quello che il creatore della DS definisce un ‘pannello bilanciato‘ ossia dell’accoppiamento di sei fogli di legno da due strati: due di taglio trasversale e uno longitudinale, piegati in modo tale da eliminare qualsiasi tensione interna e ricreare una solidità paragonabile a quella del massello.
Tutti i tom hanno lo stesso spessore salvo quelli da 10″ e da 14″, come anche il fusto dei rullanti da 14″. Spessori diversi anche per floor tom da 18″ e cassa dello stesso diametro.
Il modello di riferimento è dato dai fusti Keller utilizzati da DS per le sue batterie nel ’95, tamburi che univano due fogli dalle vene corte con un foglio dalla vena lunga, per ottenere un pitch più alto. Utilizzando fogli con due vene corte con in mezzo uno dalla vena lunga invece si ottiene un pitch più basso o ‘sordo’.
Oggi Deorsola è tornato alla concezione dei fusti del ’95, salvo che per il rullante, più fermo.
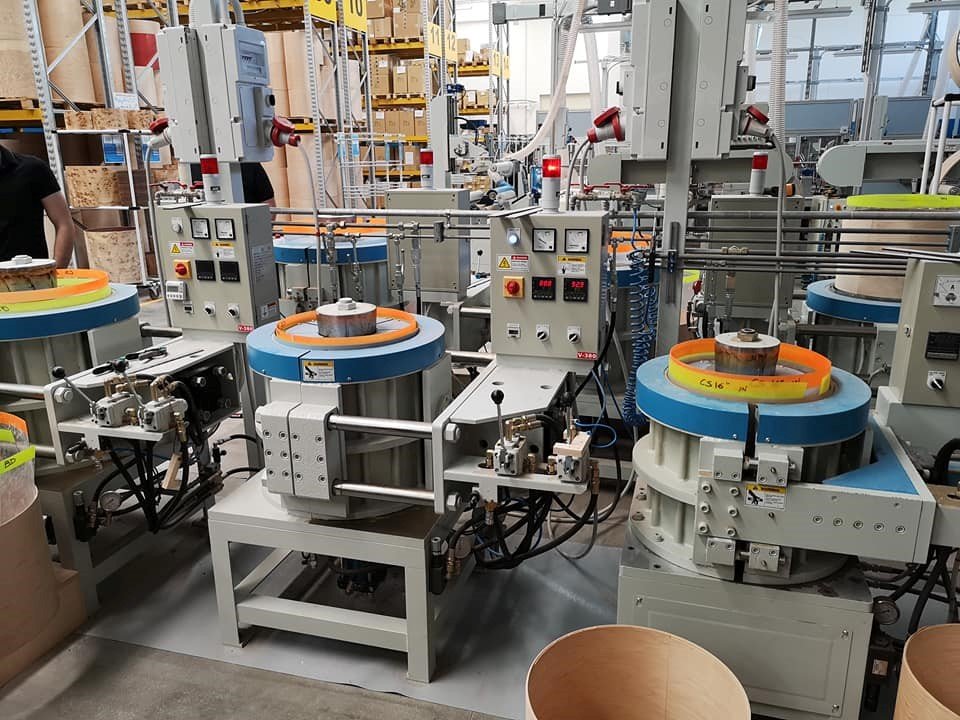
Presse per la creazione di fusti – Foto di Alessandro Dondi
Per trasformare i fogli in fusti si usano dei macchinari unici in Europa, che consentono una produzione veloce e di qualità: nelle presse i fogli sono sottoposti a temperaure di circa 90° (per far evaporare l’acqua contenuta nella colla) e a una pressione di circa 8 KG per cm quadrato (per far uscire l’aria). Trasformati in cilindri, una volta usciti dalla pressa i fusti non vengono raffreddati artificialmente per affrontare la successiva fase di lavorazione: si preferisce piuttosto prolungare il tempo di raffreddamento di alcuni giorni per far asciugare completamente la colla.
Il cilindro grezzo passa poi per altre quattro macchinari, controllati da un unico operatore, che a regime potranno lavorare circa 4/500 fusti al giorno. In questa fase i fusti vengono tagliati alla misura desiderata, viene praticato lo scavo del bearing edge (l’avvallamento del bordo per l’alloggiamento della cordiera), viene effettuata la carteggiatura e la verniciatura interna, la calibratura; la carteggiatura esterna ripulisce il fusto da residui di colla o altre impurità.
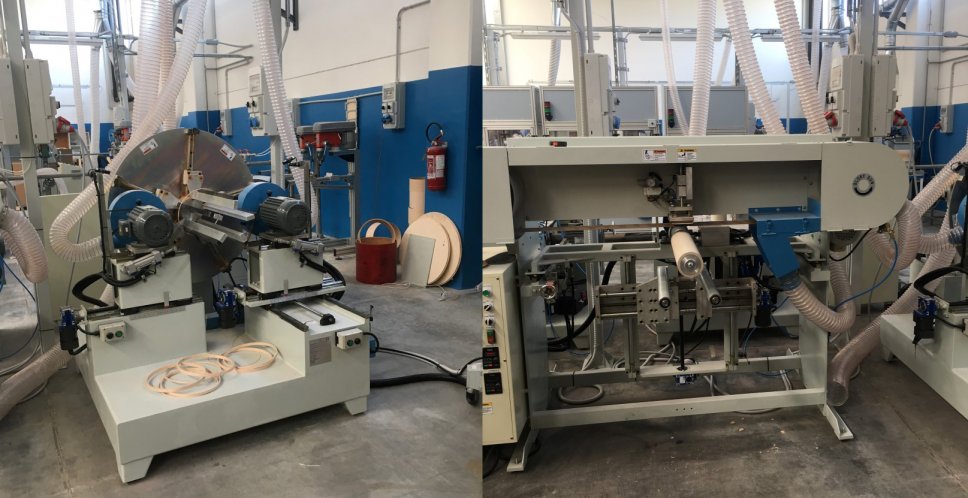
A sx la macchina per il taglio dei fusti, a dx la macchina per il carteggio
A proposito del taglio del bearing edge, val la pena ricordare che le macchine deputate sono state progettate dallo stesso Luca Deorsola. Per il rullante, l’idea di base è quella per cui minore è il contatto tra pelle risonante e fusto e migliore sarà il suono; in genere il bearing edge tende a riprodurre il taglio dei bordi (quindi 30° o 45°).
Detto che i fusti di una batteria DS non presentano cerchi di rinforzo, per quanto riguarda i bordi sono tagliati in genere a 30° tranne che per il tom da 8″, che ha i bordi tagliati a 45°. Per il rullante il taglio dipende dal suono che si vuole ottenere e dalla pelle che dovrà montare.
Dopo essere passati per le macchine foratrici, i fusti ‘subiscono’ la lucidatura e il carteggio (automatici) delle parti interne verniciate, quindi entrano nelle cabine deputate alla verniciatura estern, eseguita con macchinario robotico attraverso quattro successivi passaggi, due di verniciatura e altrettanti di asciugatura.
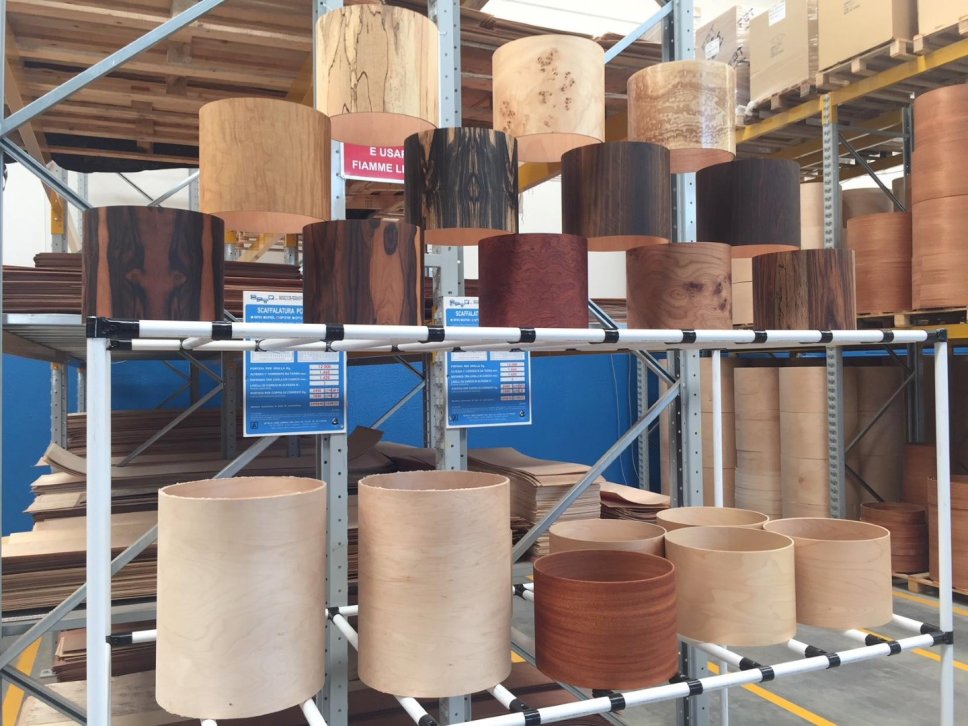
Fusti realizzati con essenze esotiche – Foto di Bendetto Zeverini
Ai tamburi vengono quindi aggiunte le parti meccaniche, tutte progettate e disegnate da Deorsola, dai cerchi ‘a effetto’ die-cast alle sfere, i blocchetti che alloggiano i tiranti, realizzati da un fornitore marchigiano e migliorati nei dettagli interni per consentire una resa ottimale anche a tensioni minime e rendere impossibile che le viti tiranti siano montate storte.
Una caratteristica distintiva delle Rebel Custom Shop sono i cerchi della cassa in mogano, quasi una ‘firma’ che accentua il design ‘caldo’ dello strumento. I tom montano pelli Remo Ambassador sabbiare sia battenti sia risonanti (come nei tamburi del ’95) per la loro facilità di accordatura e il loro suono più controllato.
Una volta assemblati, i tamburi di ogni nuova batteria vengono sottoposti a un accurato controllo di qualità (checklist), prima di venir spediti a destinazione.
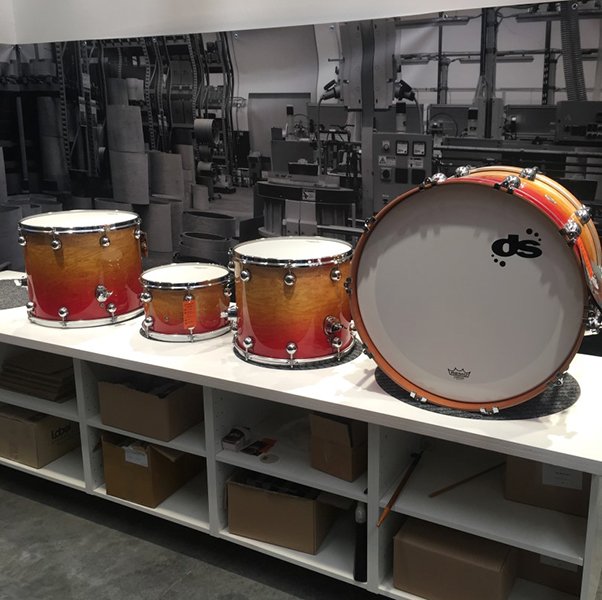
Il tavolo del controllo finale – Foto di Benedetto Zeverini
Resta da dire della produzione dei rullanti in metallo, attualmente limitata a tre diversi materiali: alluminio (un pezzo unico), acciaio e bronzo (due pezzi saldati). Per tutti la misure è – a giudizio di Deorsola – la più versatile, ossia 14″ x 6″, cui si aggiunge il 13″ x 7″ esclusivamente per i modelli in acciaio.
Le batterie DS Drum sono prodotte e distribuite da FBT Elettronica.
Aggiungi Commento